One of the reasons why our company is chosen by electric wire manufacturers is our ability to offer custom and bespoke development. We develop tailor-made tapes that meet your specific requirements, which is something that large manufacturers of electric wire tapes cannot accommodate.
Custom Development Examples
Achieving 1mm slit processing of PET film + PET adhesive
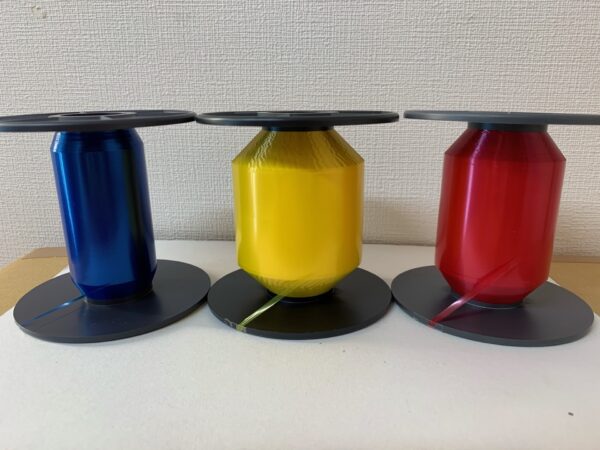
Industry | Medical、Electronics |
---|---|
Cables | Coaxial Cables |
Using for | Insulating tape for ultrafine coaxial cables |
Although coaxial cables with a fine diameter of φ0.08 traditionally faced challenges in miniaturization due to the 50 µm thickness of conventional insulation materials, the use of PET film + PET adhesive insulation tape, combined with our processing technology, allows for the reduction of the substrate and adhesive to a thin film of approximately 3.5 µm to 7.5 µm. This breakthrough enables the successful miniaturization of the cables.
Achieving ultra-thin and ultra-fine PET+AL tape
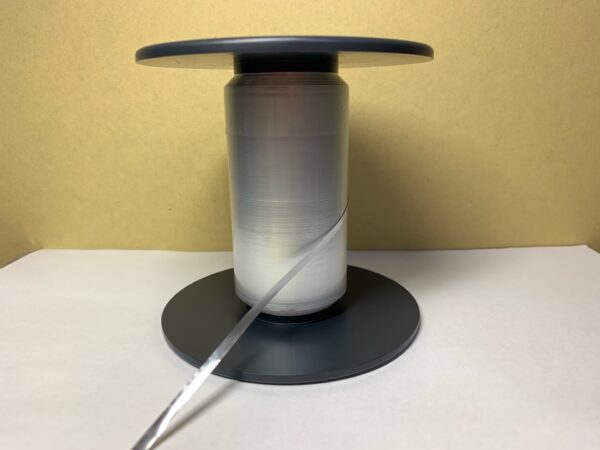
Industry | Electronics、Automotive、Data center、Robotics、Construction |
---|---|
Cables | Ultrafine coaxial cables |
Using for | Noise-shielding tape for ultrafine coaxial cables |
Our strength lies in micro-slit processing of ultra-thin and ultra-fine
We respond to customer requests and have achieved thin film processing with a tape width of 0.6 mm.
Even in the case of conventional thickness specifications of PET: 12㎛ and Al: 10㎛, we can deliver PET: 2.5㎛ and Al: 7㎛ through our processing.
We have an advantage in micro-slit processing that other companies cannot offer. If you are looking for a processing contractor for ultra-fine and ultra-thin film processing, please contact us.
Heat resistant shield tape for automotive
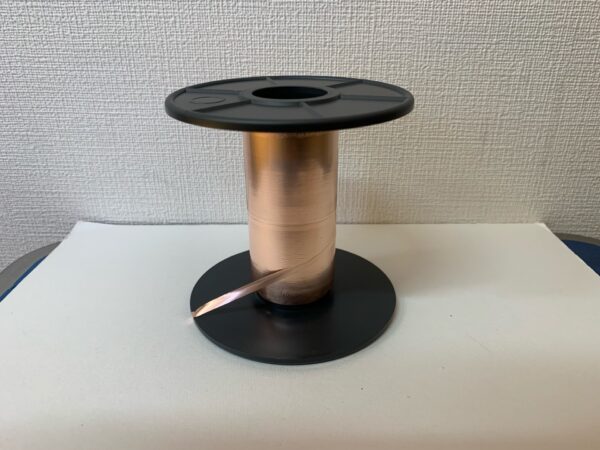
Industry | Automotive |
---|---|
Cables | Heat-resistant shield tape |
Using for | Shield tape |
◆Problem
Customers had problems with insufficient heat resistance, melting of the base material and adhesive, and peeling of the laminate layer.
◆Condition
“The film must not be damaged or peeled off after an environmental acceleration test at 150°C for 1,000 hours” on the premise that the functional requirements such as dielectric properties would be met.
◆Actions and Countermeasures
Therefore, we proposed several combinations of base materials, adhesives, and layer configurations that we assumed would satisfy the above conditions. We then conducted tests in a heat-resistant environment and selected a tape that would not break, peel, or discolor.
The final product was a combination of Cu special metallic foil and heat-resistant film (PI), delivered in 2,000 m bobbin-wrapped rolls.
Thinner copper foil film from 30㎛ to 25㎛ for flat cable
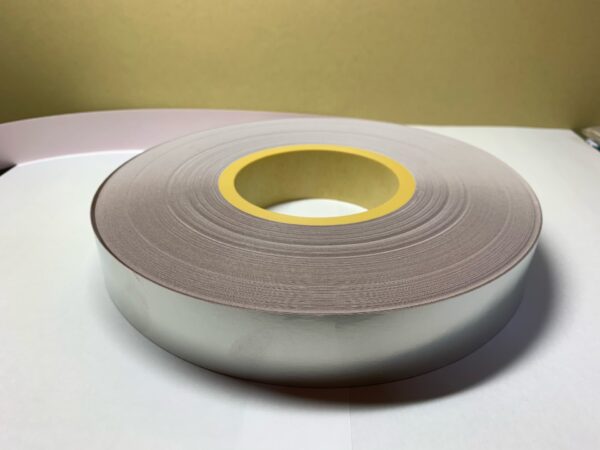
Industry | Cunsumer |
---|---|
Cables | Flat Cables |
Using for | Gland bar member for flat cable |
◆Customer’s Problem
A customer who uses functional tape as a gland bar component for flat cables consulted us about reducing the thickness of their gland bars.
Specifically, the customer wanted to solve the following problems (1) to (3).
(1) The copper foil is about 30㎛, and when combined with the adhesive, the thickness is more than 60㎛.
(2) The copper foil is 30㎛ thick, and there is a risk of delamination when stress is applied.
(3) Thick copper foil is expensive.
◆Actions and Countermeasures
We proposed a functional tape with 25㎛ copper foil and 30㎛ adhesive layer. By reducing the thickness of the copper foil by 5㎛, the aforementioned problems (1) to (3) can be solved.
The customer was concerned about quality deterioration such as precision variation due to the reduction of the thickness to 30㎛ or less, but there was no deterioration in quality and the customer was very satisfied with this case study.
Kashinoki Seisakusho, which operates the Problem Solving Center, specializes in thin-film processing of metallic film. Thin-film processing makes it possible to achieve high added value such as miniaturization and cost reduction. We can handle thin-film film processing, which is difficult for other companies to do.
Partially adhesive specification of hot melt for flat cable
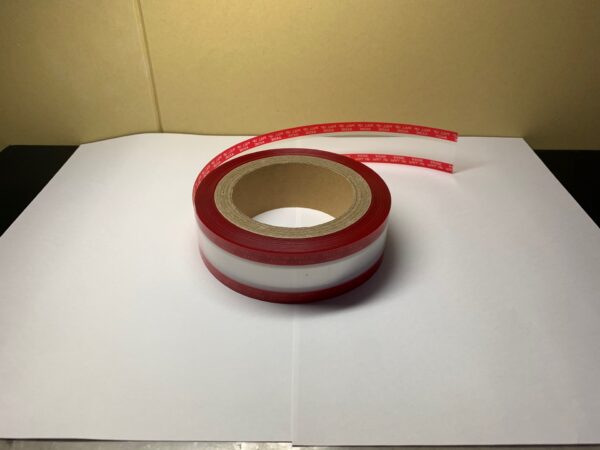
Industry | Electronics |
---|---|
Cables | Flat Cable |
Using for | Flat Cable |
We received a consultation regarding a handle for handling flat cables.
A handle was needed for handling flat cables when mounting connectors, and a functional tape was used as a handle by wrapping it around the cable.
However, the use of an adhesive tape would cause the tape to peel off even at room temperature, so we proposed using a hot melt sheet to laminate the tape together.
The tape width is 3 mm, and it is difficult to make the hot-melt sheet narrower, which is a process often avoided by competitors due to the high degree of difficulty of lamination.
In addition, we needed to print a pattern on the tape to put the customer’s logo on it, but since it was a small lot and we needed to improve the yield rate, we used a small coating machine to handle the job.
Kashinoki Seisakusho, which operates the Functional Tape and Film Processing Problem Solving Center, can handle narrow slit processing, coating, and laminating using hot melt sheets, as shown in this case.
25㎛ high-performance polyolefin resin tape to meet PFAS regulations
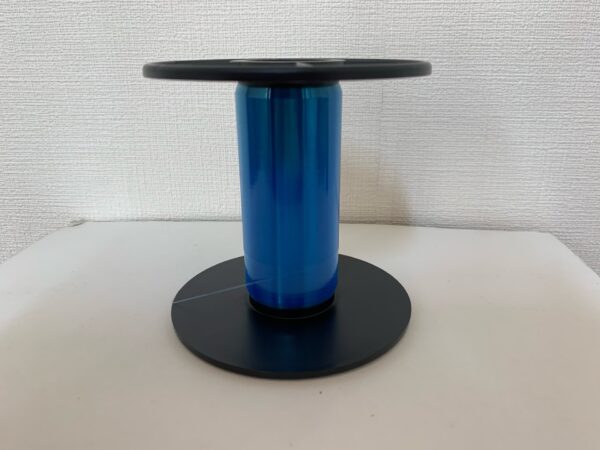
Industry | Medical |
---|---|
Cables | Shield tape |
Using for | ー |
◆Customer’s Problem.
A medical equipment manufacturer consulted us about changing the material of fluoroplastic used for high-speed transmission cables to comply with PFAS regulations. The requirements were that the dielectric constant and heat resistance be equivalent to fluoroplastic and that there be no functional problems.
◆Actions and Countermeasures
We proposed selecting a high-performance polyolefin resin and processing it.
High-performance polyolefin resin is a product generally available on the market as a process material for flexible circuit boards, but the 50㎛ requested by the customer was not sufficient for the cable specifications in this case, and an even thinner film was needed to meet the functionality requirements. Therefore, we developed and proposed a custom-made 25㎛ film in cooperation with a material manufacturer.
Compliance with PFAS regulations
Replacement with a resin that has the same functions as fluoroplastic
Thin film
This is an example of a case in which a customer was very satisfied with the result of realizing the following.
Kashinoki Seisakusho, which operates the Problem Solving Center for Functional Tape and Film Processing, is capable of handling everything from base material proposals, and has been chosen as a partner to solve customers’ problems. If you have a clear idea of the functionality you are looking for, but don’t know what kind of base material to select…, please feel free to contact us.
Delivery of 100m polyimide tape Minimizing MOQ
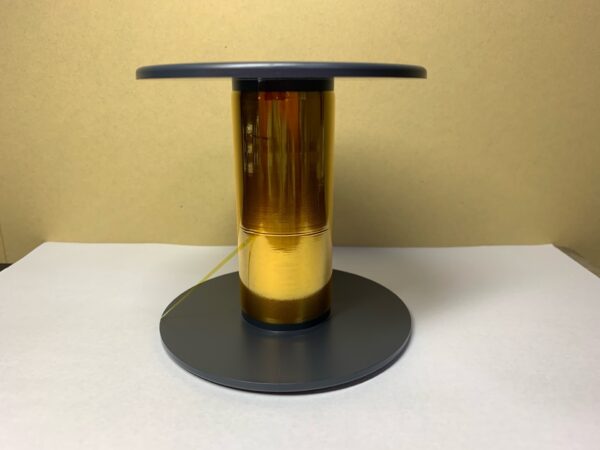
Industry | Medical |
---|---|
Cables | Shield tape |
Using for | Shield tape |
◆Customer’s problem
A customer who uses polyimide tape as shielding tape for electrical wires asked us if we could purchase polyimide tape in small lots, as their current supplier has a large MOQ and can only purchase in bulk units.
◆Actions and Countermeasures
The requested polyimide tape specifications were W0.6mm, t3,5,7.5,12.5,25μm, and several other types, and the requested purchase unit was 100m to 3000m.
We are able to deliver polyimide tape in small lots, and we were able to provide it according to the customer’s requirements.
This is an example of how we were able to reduce inventory management costs because we were able to reduce the MOQ, and the customer was very satisfied with our service.
Proposal for base material and adhesive (conductive hot melt) to improve shielding performance
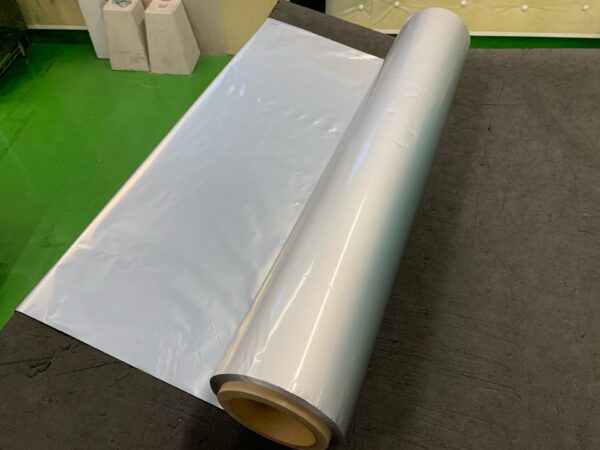
Industry | Electronics |
---|---|
Cables | Flat Cables |
Using for | Flat Cables |
We received a request for a ground connection tape for flat cables. The tape had been pattern-coated with adhesive, but the connection to the GND was unstable, so the customer was looking for a method that could bond the entire surface.
In this case, considering the required shielding performance, PET+Al was selected as the base material. For the adhesive, we proposed a conductive hot melt considering the number of lots and productivity, based on the premise that the adhesive can be applied to the entire surface of the tape.
If the heat resistance of the insulator is low, for example, and if heat is to be avoided during processing, conductive adhesive can be selected instead of conductive hot-melt.
Special corrosion-resistant copper foil that does not discolor or deteriorate in a heat-resistant environment
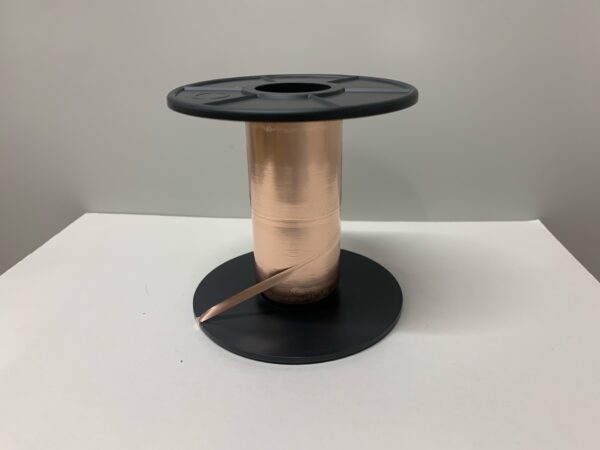
Industry | Electronics |
---|---|
Cables | Wires Cable |
Using for | Tape for high-frequency wires, tape for heat-resistant wires |
◆Customer’s problem
A customer who uses functional tapes for electrical wires requested us to propose a copper tape that does not discolor even in a heat-resistant environment.
The customer had previously used tough pitch copper (C110), but this discoloration occurred when exposed to a heat environment, and the customer was concerned about the negative impact on quality.
◆Actions and Countermeasures
We discussed specifications with our copper foil partner and considered using a special rust-proof copper foil used for other applications instead of copper foil for electric wires. We manufactured a prototype of copper foil for electric wires that had undergone a heat treatment process and tested it by simulating the customer’s environment.
The customer’s requirement was “no discoloration even after aging at 125°C for 240 hours.” We confirmed that there was no discoloration or change in resistance value under the relevant conditions, leading to mass production.