Oak-trees,Inc. is dedicated to developing technologies for film processing and tape processing to solve issues related to tape and film for electric wires. As a tape processing manufacturer that tackles challenging problems, we provide unique value to our global partners that other companies cannot offer. If you have any issues, please feel free to consult with us.
Challenges addressed
through technology development
- Heat resistance
- Electrical insulation
- Dielectric properties
- Weather resistance
- Flame retardancy
- Processability
- Durability
- Miniaturization and weight reduction
- Cost reduction
Scope of technology development
Our company handles everything from the research and development of adhesives and substrates to the development of processing technologies, including micro-slit processing and lamination processing.
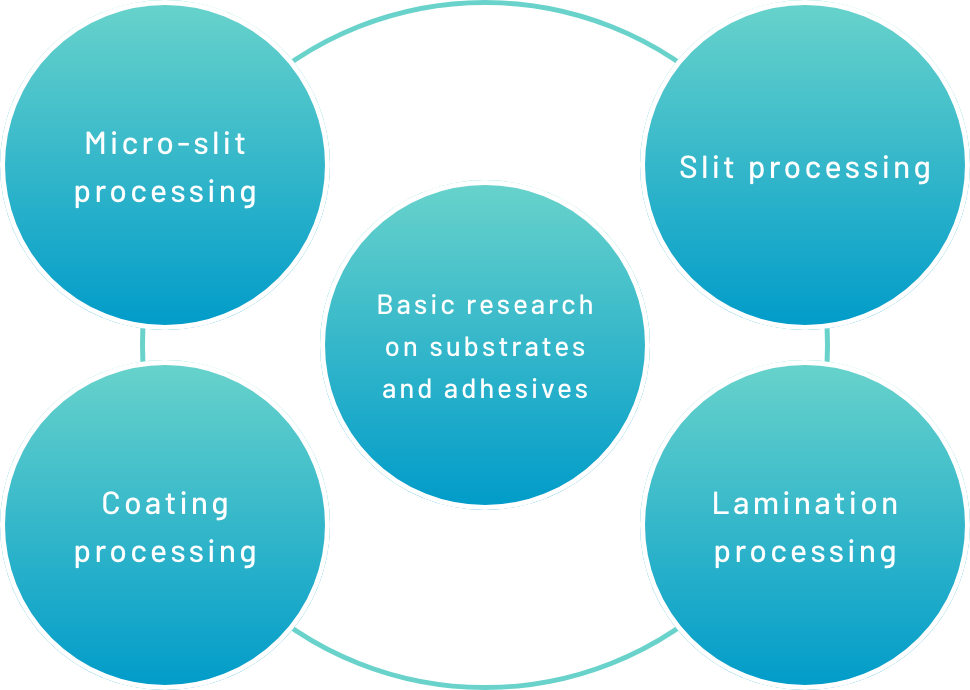
Our proprietary technologies
Micro-slit processing of thin films with a thickness of 2.5 µm

<Our proprietary technologies>
●Customized equipment specialized for processing ultra-thin film
●Condition setting and processing know-how cultivated through years of thin film processing
●Quality assurance through our extensive inspection facilities
Why is the processing of thin film considered to be highly difficult?
(1) The thinner the film, the more difficult it is to handle.
(2) Film transport is unstable and accuracy varies.
When the film thickness reaches 2.5㎛, it is difficult to handle with ordinary microslitters, and the accuracy is not stable. For this reason, we have installed our own custom-made microslitters to handle 2.5㎛ film processing, enabling us to set conditions specifically for low-tension conveyance and thin films.
The power of our custom-made microslitters and the processing technology we have cultivated over the years enable us to achieve high-precision, high-quality processing of thin-film films.
We provide high-quality products to our customers by possessing digital microscopes, image dimensional measuring instruments, and laser elemental analyzers to ensure quality.
<Using for>
Material: PET ⇒ Application: Ultrafine coaxial cables
Material : PET PP ⇒ Application : Film capacitor
Material: PET ⇒ Application: Jig for adjusting percussive force for film processing
Finishing of long lengths exceeding 20,000 meters
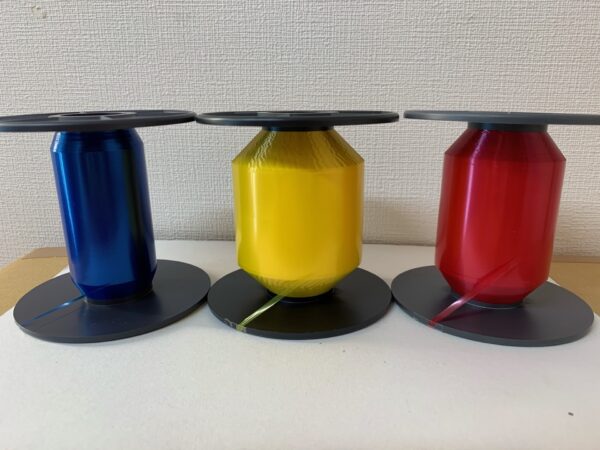
<Our proprietary technologies>
●Custom-developed cores capable of handling long rolls of 20,000 m or more
●Technology capable of handling film processing with a thickness of 2.5 μm
We develop custom-made cores to accommodate long rolls of 20,000 m or more. We have not only one type of custom-ordered cores, but also multiple types of cores to meet customers’ requirements such as roll volume and roll shape.
In addition, we often receive requests for long rolls, especially for thin film, but the thinner the film, the more difficult it is to handle and the more likely it is to lose its final shape when rolled.
We have expertise in low-tensile processing and can provide high-quality final products in rolls of 20,000 m or more.
<Using for>
Material: PET ⇒ Application: Ultrafine coaxial cables
Material : PET PP ⇒ Application : Film capacitor
Material: PET ⇒ Application: Jig for adjusting percussive force for film processing
t2.5㎛ PET film coating process
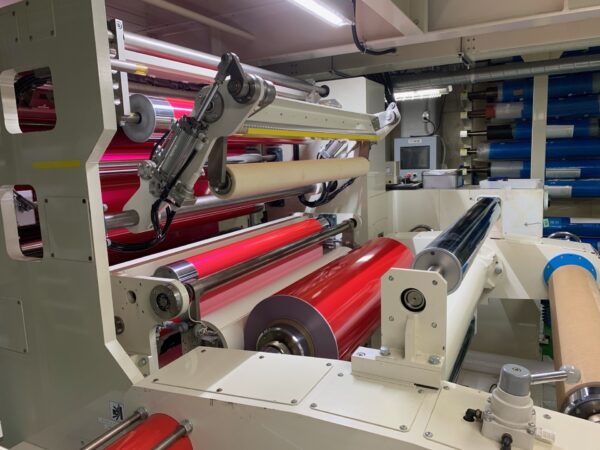
<Our proprietary technologies>
●Possesses know-how of film winding and conveying at low tension
●Small coating machines capable of coating narrow 80 mm widths
●Development capability to thoroughly coordinate specifications with material manufacturers, even for difficult specifications
●Appropriate temperature and humidity control of materials for stable and accurate processing
Film coating processing refers to the application of adhesives and other materials to film substrates. When coating processing ultra-thin materials with a thickness of 2.5 µm, thin films are sensitive to tension and are difficult to control, requiring detailed adjustment of processing conditions. Kashinoki’s coating equipment is capable of low tension control and is suitable for processing thin materials. The conditions under which ink dries are also defined in detail, enabling processing without thermal shrinkage or thermal stress. This allows us to provide products that maintain elongation and strength.
<Using for>
Material: PET ⇒Application: Ultrafine coaxial cables
Material: PET PP ⇒Application: Film capacitor
Material: PET ⇒Application: Film processing jig for percussion adjustment
Thin laminate processing (2.5µPETx6µCU)
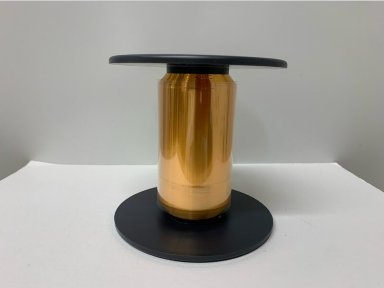
<Our proprietary technologies>
●Realization of ultra-thin laminate processing using custom equipment specialized for low tensile strength
●Establishment of appropriate processing conditions and quality evaluation with our well-equipped inspection and analysis equipment
●Selection capability based on extensive knowledge of ink characteristics through our accumulated development experience
Thin laminate processing utilizes precision coating technology. Typical laminate processing issues include (1) adjusting the specifications of materials such as film and adhesive, and (2) establishing and managing appropriate processing conditions.
For issue (1), we work closely with material manufacturers in the development stage to select appropriate materials.
For issue (2), we utilize our accumulated development know-how to establish ink drying conditions and appropriate winding conditions to realize proposals that meet customer requirements.
<Using for>
Material: PET Applications: Ultrafine coaxial cables
Material: PET Purpose: Jig for adjusting perpendicularity for film processing
Material: PET x NY Usage: Packaging material
Material: PET x CU Application: Noise shielding film for ultra-small space
Minimum width 0.6mm Narrow slit processing of adhesive tape
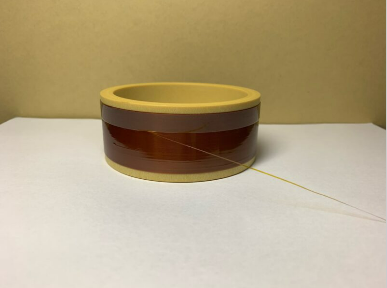
<Our proprietary technologies>
●We have built a processing line specialized for adhesive tapes, enabling high-quality slit processing without being affected by adhesive agents.
●Cutting blades are treated to avoid adverse effects of adhesive agents.
The following are the common problems with slit processing of adhesive tape
(1) Adhesive adhesive adhering to the cutter and rolls, resulting in poor quality.
(2) Decrease in processing accuracy
In order to avoid the adverse effects of adhesive, we have built a processing line specialized for adhesive tape. In addition, we apply a release treatment to the blades to prevent quality deterioration due to adhesive adhesion.
Regarding (2), we use the rewind slitting process for processing narrow widths of adhesive tape, rather than the general plunge slitting process, to achieve high-precision film processing.
<Using for>
Capacitors for Automotive
Our equipment and facilities
In addition to the aforementioned technical capabilities, we meet your requirements through the following equipment and facilities that we possess:
List of Processing Equipment
Slitter Equipment
No | Roll Width | Unwinding Load Capacity | Winding Load Capacity | Unwind Inch | Unwound Product Outer Diameter | Maximum Outer Diameter of Wound Product | Winding Inch | Minimum Achieved Width |
---|---|---|---|---|---|---|---|---|
1 | 580mm | - | - | 3Inch | 400φ | 300φ | 1Inch 2Inch 3Inch | 3mm(G5) |
2 | 580mm | - | - | 3Inch | 400φ | 300φ | 1Inch 2Inch 3Inch | 6mm(ALPET) |
3 | 780mm | 200kg | - | 3Inch 6Inch 12Inch | 500φ(560φ) | 500φ | 3Inch 6Inch | 3mm(PET9) |
4 | 660mm | 150kg | - | 3Inch 6Inch | 500φ | 400φ | 3Inch | 80mm~ |
5 | 660mm | 150kg | - | 3Inch 6Inch | 500φ | 400φ | 3Inch | 3.5mm(metal) |
6 | 660mm | 150kg | 52kg | 3Inch 6Inch | 500φ | 400φ | 3Inch | 3.5mm(PET9) |
7 | 1300mm | 300kg | 42kg | 3Inch 6Inch | 500φ~600φ | 500φ | 3Inch | 80mm~ |
8 | 1200mm | 500kg | 170kg | 3Inch 6Inch | 700φ | 400φ | 3Inch | - |
9 | 300mm | - | - | 3Inch | 270φ | 200φ | 3Inch | - |
Micro Slitter Equipment
No | Roll Width | Unwinding Load Capacity | Winding Load Capacity | Unwind Inch | Unwound Product Outer Diameter | Maximum Outer Diameter of Wound Product | Winding Inch | Minimum Achieved Width |
---|---|---|---|---|---|---|---|---|
1 | 180mm | 40kg | - | 3Inch | φ500 | Φ120 (Φ140 if no guide) | ID30.3Inch | text |
2 | 120mm | - | - | 3Inch | φ360 | - | ID30.3Inch | 1.6 |
3 | 180mm | - | - | 3Inch | φ520 | - | ID30 | 0.6 |
4 | 180mm | - | - | 3Inch | φ540 | - | ID30 | 0.6 |
5 | 180mm | 40kg | 5kg | 3Inch | φ580 | φ120 | ID30.3Inch | 0.6 |
6 | 180mm | 40kg | 5kg | 3Inch | φ580 | φ120 | ID30.3Inch | 0.6 |
7 | 180mm | 40kg | 5kg | 3Inch | φ580 | φ120 | ID30.3Inch | 0.6 |
8 | 180mm | 40kg | 5kg | 3Inch | φ580 | φ120 | ID30.3Inch | 0.6 |
9 | 350mm | 200kg | 5kg | 3Inch | φ800 | φ300 | P-30.3Inch | - |
10 | - | - | - | 3Inch | φ320 | - | P-30.3Inch | - |
Coating Equipment
Equipment Name | Substrate Width | Using for |
---|---|---|
Large Coating Machine | 500mm~1080mm | Gravure Coating, Dry Lamination |
Small Coating Machine | 80mm~500mm | Gravure Coating, Knife Coating, Dry Lamination |
Heat Laminator
No | Usage Temperature | Preheat Roll Temperature | Width | Core Diameter | Maximum Original Roll Diameter (Substrate Side) | Maximum Original Roll Diameter (Dry Side) | Maximum Winding Diameter | Pressurization Method |
---|---|---|---|---|---|---|---|---|
1 | Max150℃ | 100℃ | 550mm | 3Inch(6Inch for Raw material side) | φ700 | φ500 | φ350 | Air Cylinder |
Rewinder
Roll Width | Unwinding Diameter | Winding Diameter | Strap Winding Diameter | Core Diameter | Tension | Load Capacity |
---|---|---|---|---|---|---|
200mm | φ450mm | φ350mm | φ450mm | 3Inch | 10~40N | 30kg |
List of Inspection Equipment
Equipment Name | Manufacturer Name | Model Number |
---|---|---|
Digital Microscope | KEYENCE CORPORATION | VHX-7000 |
Ultra-Depth Multi-Angle Lens | KEYENCE CORPORATION | VHX-D510 |
Shape Analysis Laser Microscope | KEYENCE CORPORATION | VK-X1000 |
Laser Element Analysis Head | KEYENCE CORPORATION | EA-300 |
Image Dimension Measurement Device | KEYENCE CORPORATION | IM-8030 |
Dielectric Measurement Device | AET, Inc. | Cavity Resonator |